Subscriber Exclusive
Clematis Lace
A small amount of finely spun cotton knits up into a classic lace doily. Learn why sizing the yarn before or after knitting can help combat wear and tear.
A small amount of finely spun cotton knits up into a classic lace doily. Learn why sizing the yarn before or after knitting can help combat wear and tear. <a href="https://spinoffmagazine.com/clematis-lace/">Continue reading.</a>
https://spinoffmagazine.com/cdn-cgi/image/format=auto/https://www.datocms-assets.com/75073/1656685921-clematis-lace-1.jpg?auto=format&w=900
It’s only a matter of time before new spinners attempt to spin fine yarns. And cotton enthusiasts like me are constantly inspired by the endless possibilities of cotton in the textiles around us. Not long after I began spinning cotton, I found an unusual cotton sliver at a fiber festival and wondered, “Could I—should I—try to spin this luxurious fiber into a fine thread?”
I had been searching for natural-color cotton at the festival when I found a small quantity of recycled denim sliver. The fine, short-stapled fiber was a blend of various hues of light indigo with tiny flecks of navy throughout. I loved its painterly effect; a special yarn would come from this fiber.
Spinning Notes
Wanting to create as much yardage as possible from the small 1-ounce bag of fiber, I set out to spin my finest cotton yarn ever. My tool of choice was a supported spindle for maximum control. I carefully hovered over every inch of long-draw singles to smooth even the tiniest slubs. I spun the singles with a lot of twist and pressed the loft out of the fiber as I went, creating a smooth yarn with a defined surface.
After spinning the singles, I used my Kromski Sonata spinning wheel set on a 14:1 ratio to create a two-ply yarn, letting the twist build up until the yarn felt firm. The resulting yardage was dense, durable, and round like crochet cotton.
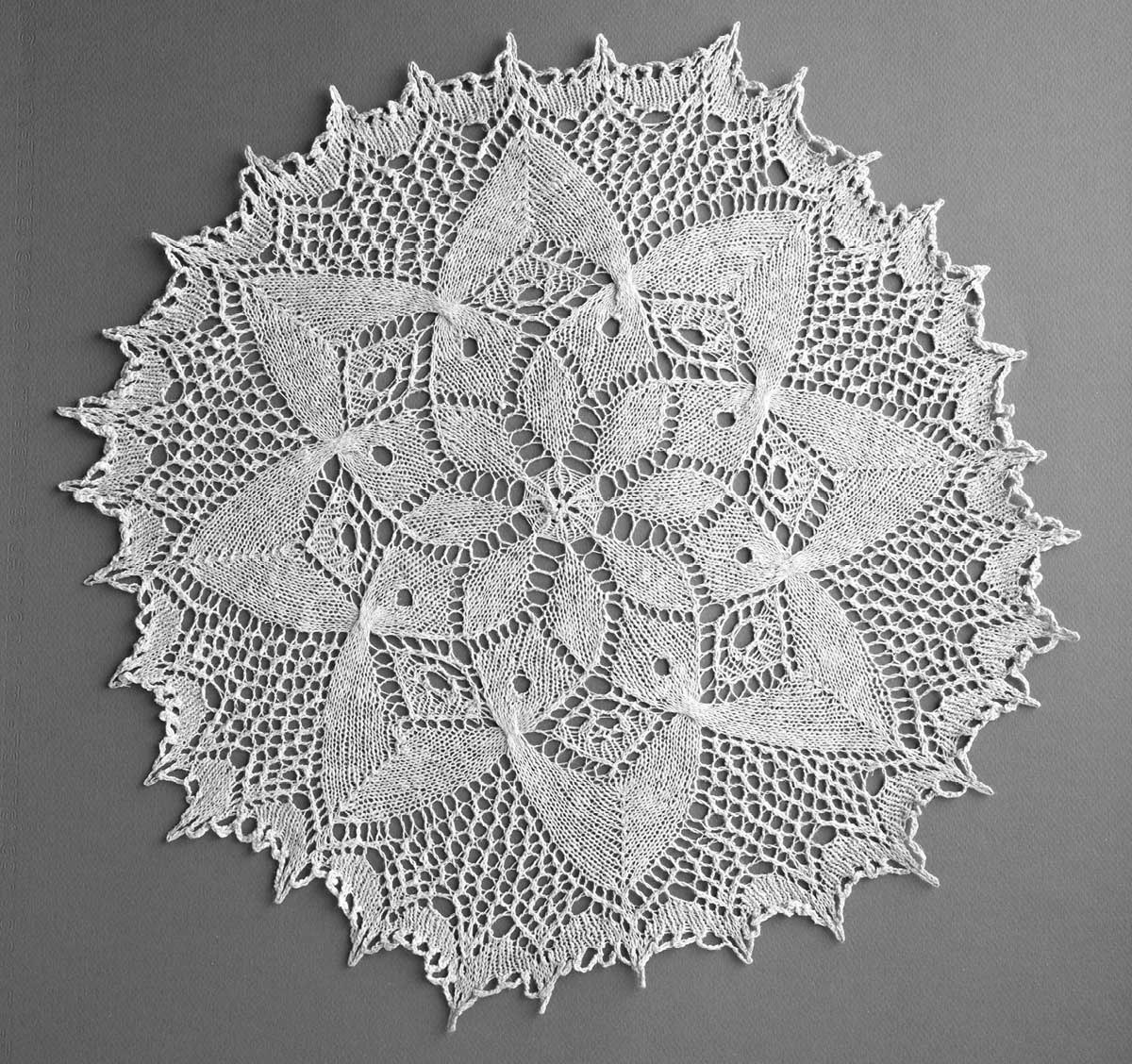
After knitting from the center out, all stitches are crocheted off. Photo by Matt Graves
Initially, I was tempted to pack the 300 yards of cotton laceweight away like countless other precious handspun skeins; I couldn’t do that with this one. The yarn was so unique and rare that I had to see it worked up right away. At first, I thought I’d crochet some snowflake ornaments but decided the yarn’s handspun allure would get masked in the compact intertwinement of crochet stitches. I really wanted to make something larger that would showcase this fine yarn; knitted lace was my answer.
SUBSCRIBER EXCLUSIVE
It’s only a matter of time before new spinners attempt to spin fine yarns. And cotton enthusiasts like me are constantly inspired by the endless possibilities of cotton in the textiles around us. Not long after I began spinning cotton, I found an unusual cotton sliver at a fiber festival and wondered, “Could I—should I—try to spin this luxurious fiber into a fine thread?”
I had been searching for natural-color cotton at the festival when I found a small quantity of recycled denim sliver. The fine, short-stapled fiber was a blend of various hues of light indigo with tiny flecks of navy throughout. I loved its painterly effect; a special yarn would come from this fiber.
Spinning Notes
Wanting to create as much yardage as possible from the small 1-ounce bag of fiber, I set out to spin my finest cotton yarn ever. My tool of choice was a supported spindle for maximum control. I carefully hovered over every inch of long-draw singles to smooth even the tiniest slubs. I spun the singles with a lot of twist and pressed the loft out of the fiber as I went, creating a smooth yarn with a defined surface.
After spinning the singles, I used my Kromski Sonata spinning wheel set on a 14:1 ratio to create a two-ply yarn, letting the twist build up until the yarn felt firm. The resulting yardage was dense, durable, and round like crochet cotton.
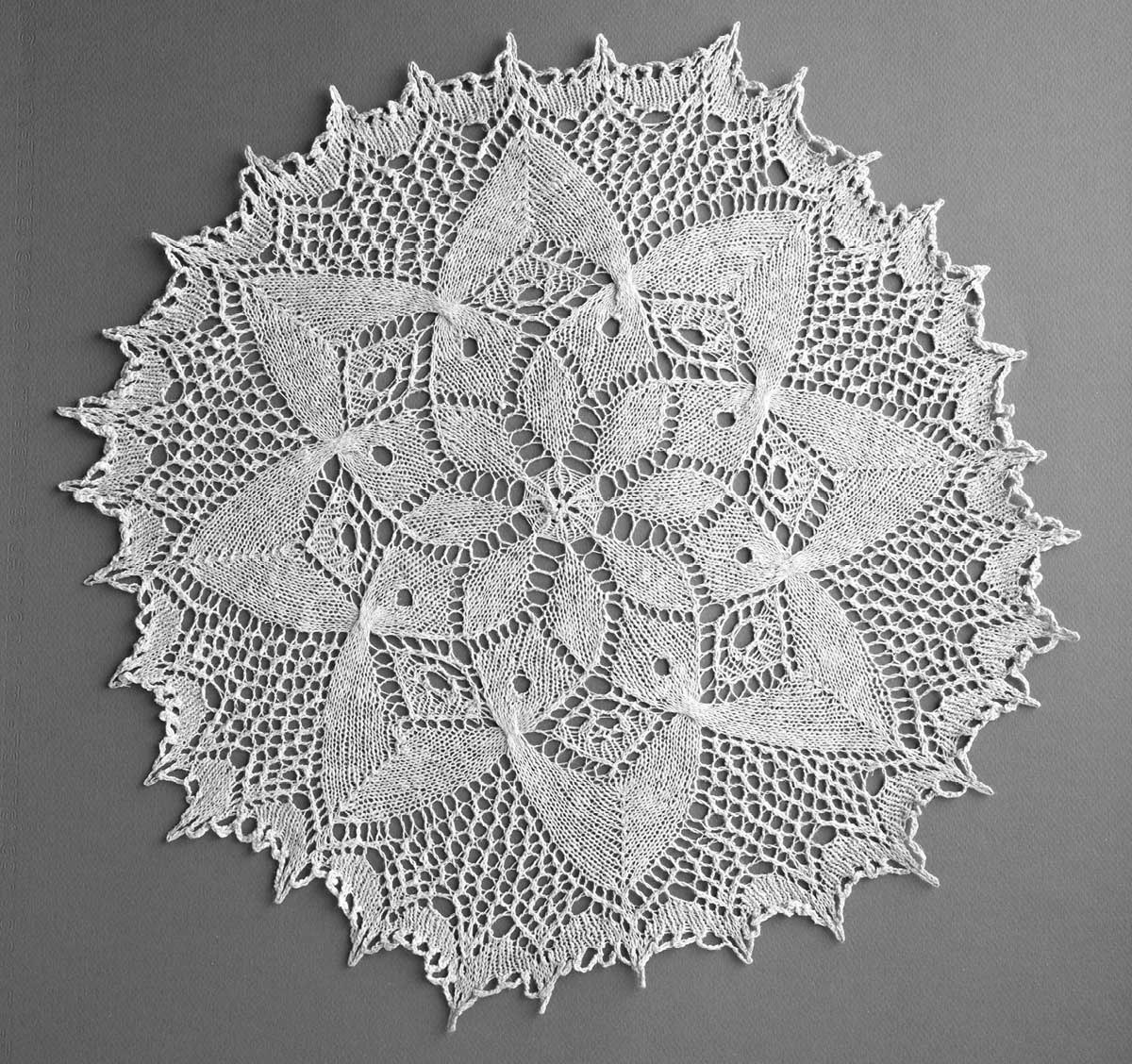
After knitting from the center out, all stitches are crocheted off. Photo by Matt Graves
Initially, I was tempted to pack the 300 yards of cotton laceweight away like countless other precious handspun skeins; I couldn’t do that with this one. The yarn was so unique and rare that I had to see it worked up right away. At first, I thought I’d crochet some snowflake ornaments but decided the yarn’s handspun allure would get masked in the compact intertwinement of crochet stitches. I really wanted to make something larger that would showcase this fine yarn; knitted lace was my answer.
[PAYWALL]
Sizing Handspun Cotton
When I want to create a crisp, structured fabric, such as in fine, knitted-lace doilies, I turn to sizing. Sizing involves coating your yarn or finished textile with a filler or glaze, and it is used for different reasons by weavers, knitters, crocheters, lacemakers, and seamstresses.
For my project, I wanted to stiffen the cotton yarn so the lace pattern would remain sharp and visible. A coated yarn will also resist abrasion and therefore last longer. Another reason you may want to use sizing on knitted handspun cotton is to help prevent permanent staining. In my experience, soil adheres to the sizing instead of penetrating deeper into the fiber.
Sizing the yarn before working a knitted project is usually not necessary. However, I have found it useful when knitting very fine, loose lace with all rows patterned. The yarn will be smoother and stiffer, holding the pattern and allowing repeated frogging in the unfortunate event that something goes awry.
For cotton intended for knitted lace, I like a sizing solution made with cornstarch. Dissolve ¼ cup (59 ml) of cornstarch into ½ cup (118 ml) of cold water. Stir the mixture into about 4 cups (0.95 L) of boiling water. Allow the solution to cool. The consistency and appearance at this point should be like clear laundry detergent. You can adjust the viscosity of the solution by adding water. Do you want to create a drapey yet crisp hand? Add more water to dilute. Are you making objects such as knitted ornaments that need to be fairly inflexible? Use the solution at full strength.
Submersion Method
When working with yarn, place your skein or knitted textile into the starch solution, allowing it to become fully submerged. Squeeze the solution through the fibers to make sure it fully penetrates. Remove the skein or textile and wring out excess liquid. If sizing yarn, snap the skein to remove any tangles or kinks and then pull it into shape. Hang the skein to dry where it can get good airflow. Rotate the skein and separate the threads frequently as it dries. For drying knitted lace, stretch and pin the piece into shape on a blocking mat, form, or frame.
Spray Method
You can also size completed knits by applying a diluted starch solution with a spray bottle. First, wet the textile with water and make sure excess liquid is squeezed out. Next, spray the piece with the diluted starch solution, pin it into shape, and let it dry. This method tends not to last as long before needing to refresh the starch, however it is effective for a light hold for perhaps a lacy summer shawl. You can refresh your knitted cotton lace in a pinch by misting it with the diluted starch mixture and lightly pressing it with an iron. It will compress the yarn a little, but this technique will keep cotton wearables nice and airy with less wrinkling and shrinkage.
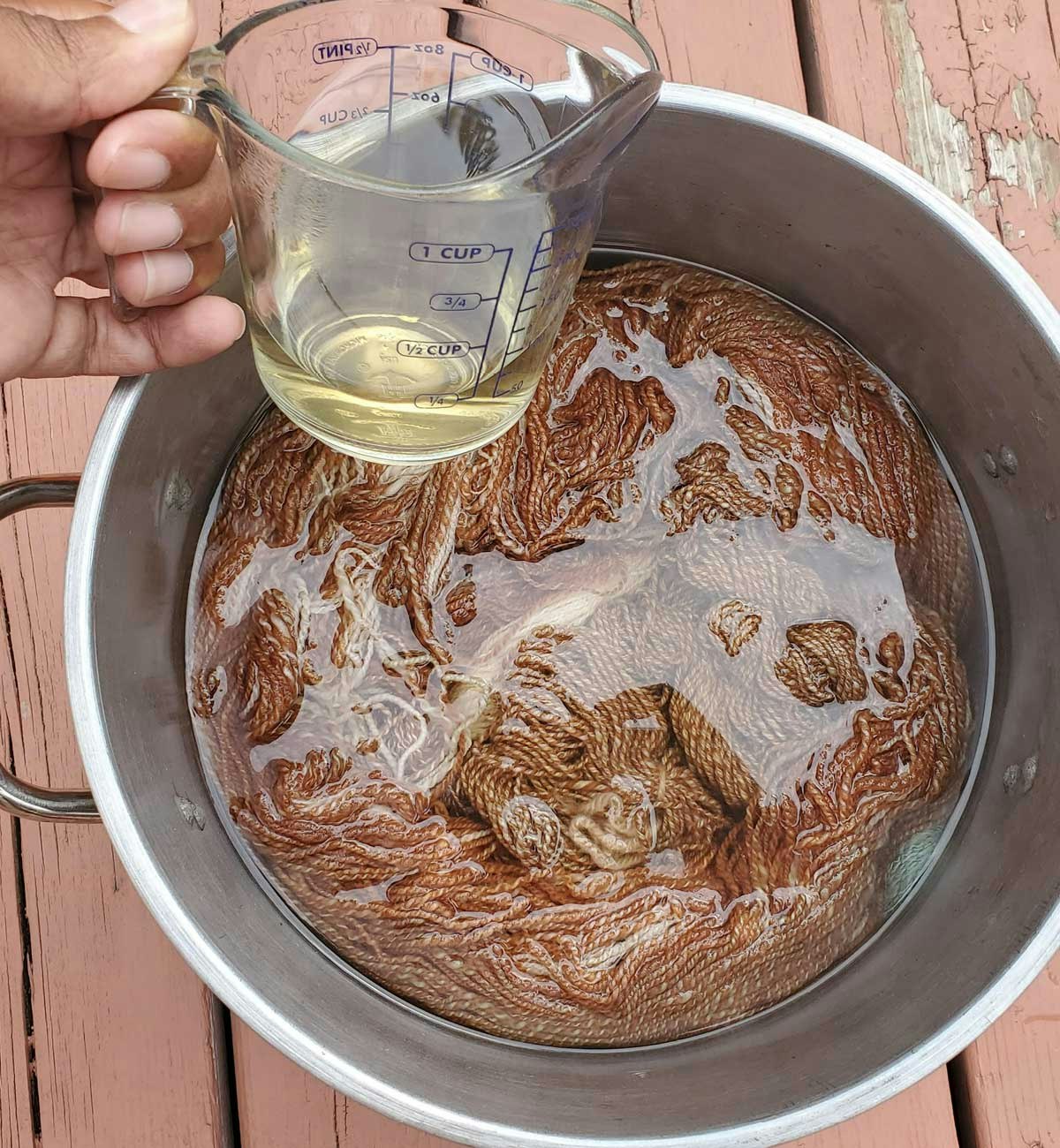
Sizing handspun cotton. Photo courtesy of Melvenea Hodges
Finishing
After spinning for this project, I washed the yarn in warm water before knitting. After knitting the doily and weaving in ends, I submerged it in a diluted starch solution and squeezed out the excess. Then, I stretched and pinned it into shape on a blocking mat and allowed it to dry.
Doilies?
Before the summer of 2010, it had never occurred to me that I would ever need or want a doily. I grew up with printed disposable napkins and tablecloths. Fancy handmade table linens—especially doilies—were not used for our special occasions. After painstakingly spinning my first skein of cotton laceweight, I finally understood why doilies were once popular to knit. They allow you to knit exquisite, complex lace using up small quantities of yarn, which means they are also perfect for showcasing cotton handspun. Doilies are to a handspinner what canvas is to a painter.
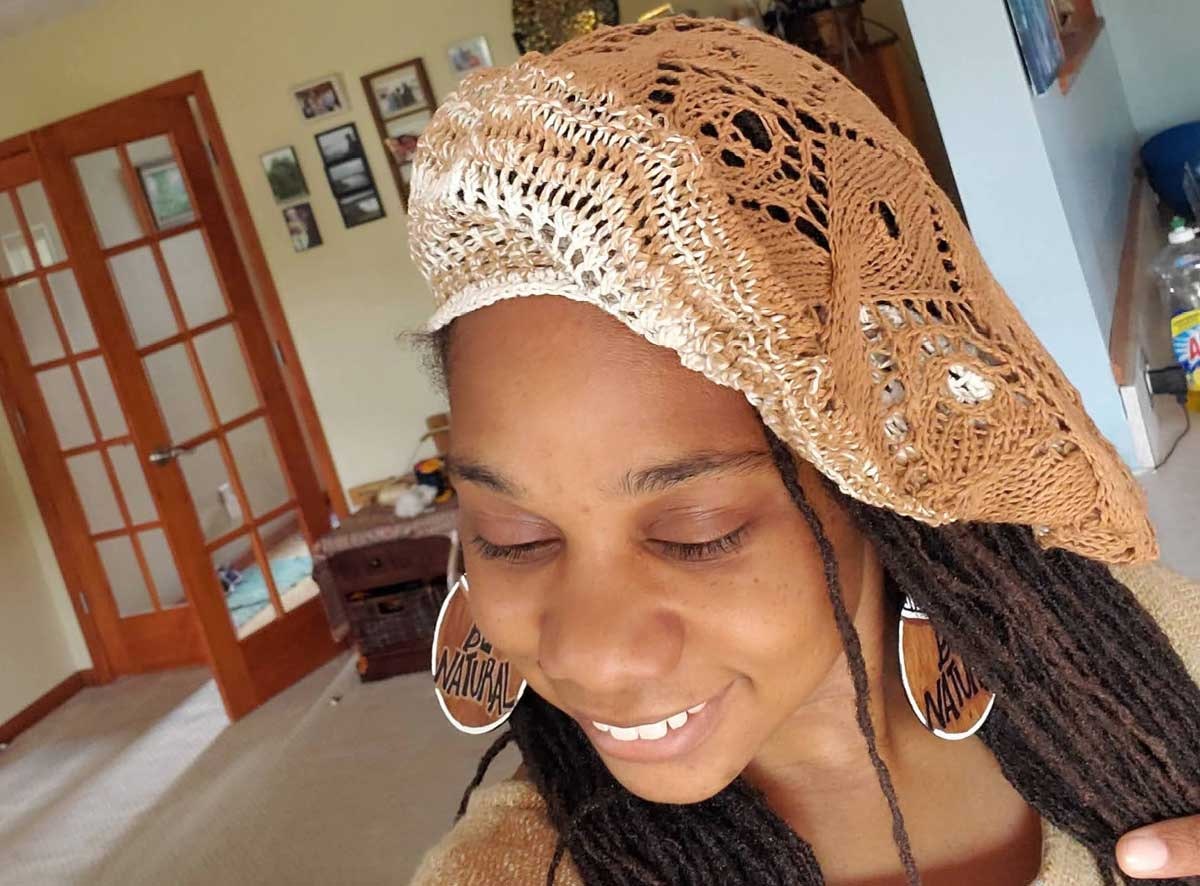
Melvenea in a beanie she created using the same doily pattern and handspun cotton. Photo courtesy of Melvenea Hodges
This project caused me to reflect upon and acknowledge my connection with the countless fiber artists before me. Our lives may be vastly different, yet we knit doilies for the same reason; we love to create and admire fiber art.
Melvenea Hodges is a fiber artist born and raised in Benton Harbor, Michigan. She is committed to practicing traditional textile techniques in honor and expression of her heritage as an American maker. She intermittently blogs about her latest creations and fiber adventures at www.traditionsincloth.com.
This pattern was previously published in Knitting Traditions, Spring 2010 as A Christine Duchrow Lace Centerpiece with a companion article about Duchrow’s art pattern knitting. The handspun version by Melvenea Hodges is available in the Fall 2020 issue of Spin Off. Melvenea's version was adapted from the Knitting Traditions version by Charlene Schurch, which was based on the original pattern by Christine Duchrow.
Materials
Fiber ⅞ ounce (25 g) recycled denim cotton sliver.
Yarn 300 yd (274 m) 2-ply; 2,100 ypp; 34 wpi; laceweight.
Needles Size 1 (2.25 mm) set of 5 double-pointed needles.
Notions Cable needle; crochet hook size B (2.25 mm); stitch markers; T-pins, blocking mat, and cornstarch for blocking.
Finished Size about 15½" in diameter depending on blocking.
Instructions
CO 8 sts and divide onto 3 needles. Taking care not to twist sts, join them into a circle and k 1 rnd. Work rnds 1 through 80 of the chart (see the chart notes for even-numbered rnds). After the first 8 rnds, redistribute the sts onto 4 needles with a m between reps for the rem of the work. Work all double yarnovers as 2 sts (k1, p1) on the subsequent even-numbered rnd unless otherwise noted.
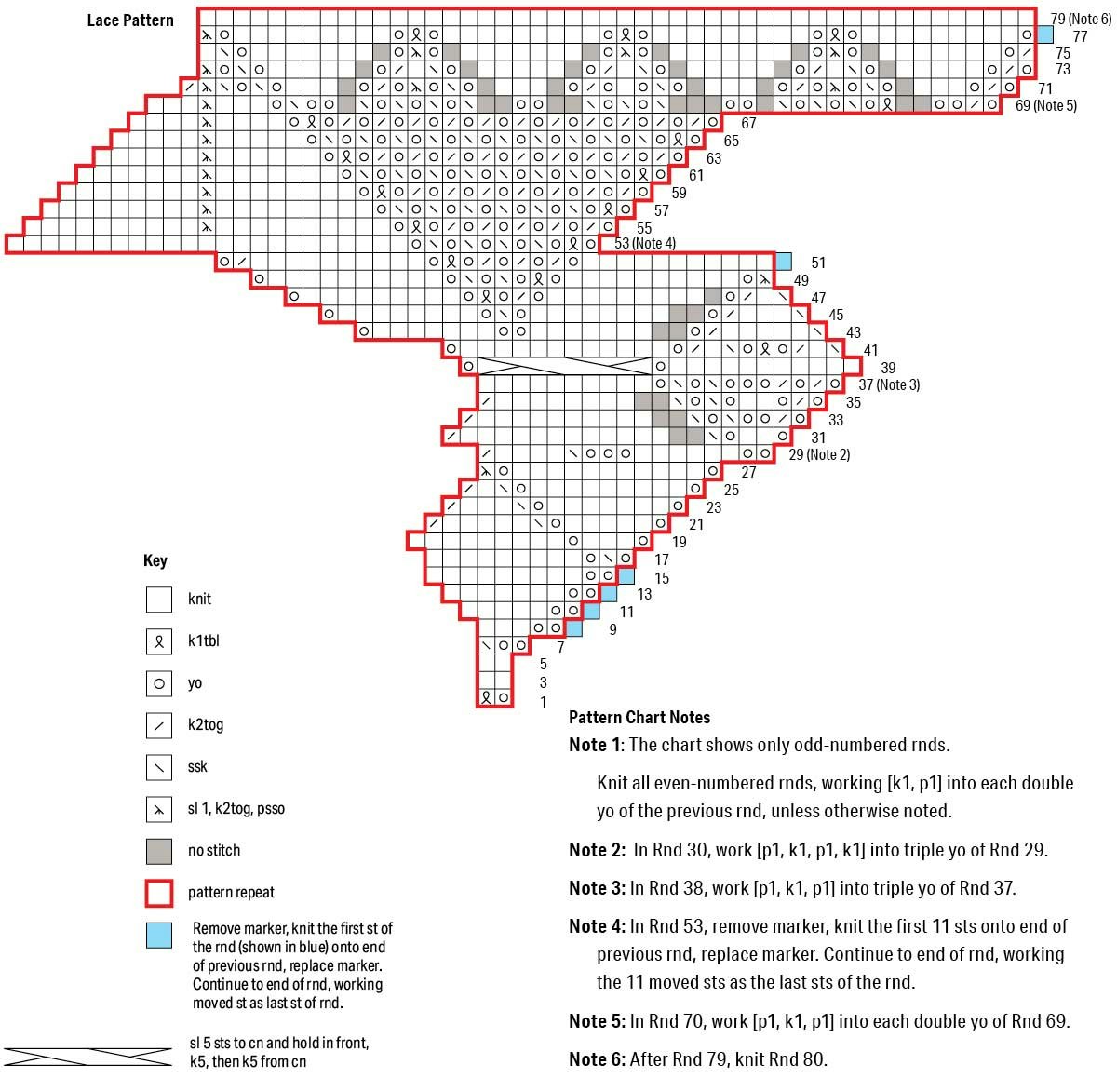
Finishing
Crochet off: *Insert the crochet hook into the next 2 sts on the left-hand needle as if knitting them tog through the back of the sts (Figure 1). With the sts still on the needle, make a sc (Figure 2), slipping the sts off the needle when the sc is completed. Ch 7. Rep from * around until all the sts have been used. Ch 7, then sc into beg sc. Fasten off and darn in any loose ends.
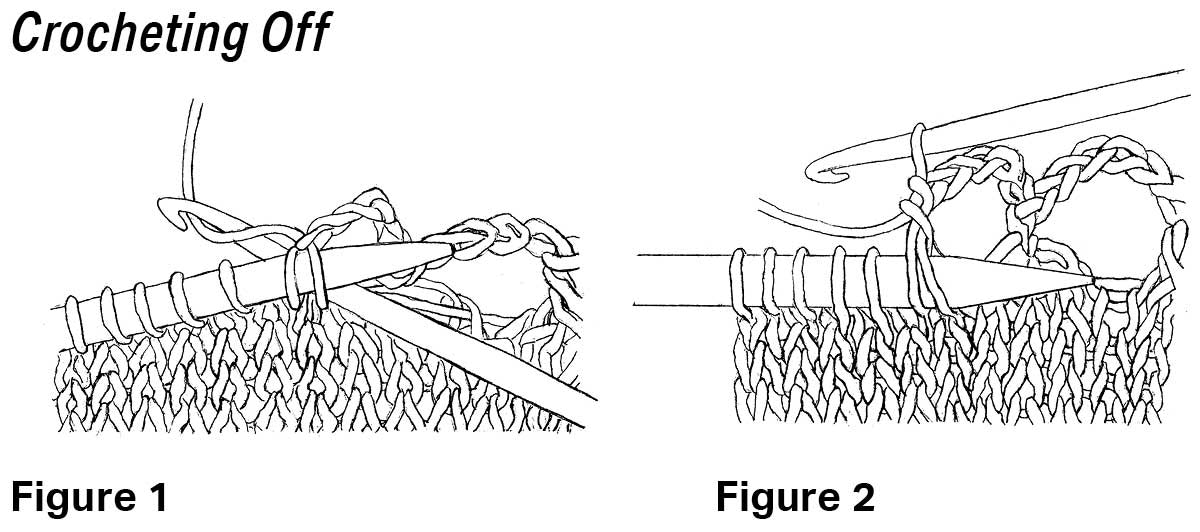
Handwash the finished piece in warm water and mild soap, and then rinse thoroughly.
Create a diluted starch solution by mixing ¼ cup (59 ml) of cornstarch into ½ cup (118 ml) of cold water. Stir the mixture into about 6 cups (1.4 L) of boiling water. Allow the solution to cool.
Submerge knitting, squeezing starch solution into the fibers, and then squeeze out excess liquid. Stretch and pin into shape on a blocking mat as follows: Pin the intervening crocheted lps into a series of arches between the petals. Adjust the pins as you work to achieve even spacing and a smooth outline. When the centerpiece is completely dry, remove the pins.